Production of ball valves for more than 23 years
About
IC Enerpred-Yardos Company was founded in 1997
Currently, the company employs 215 people, the production is equipped with more than 60 modern metal-cutting machines, and there is a laboratory for checking materials, a robotic welding section, a paint shop, an electroplating section, a heat treatment section. This makes it possible to produce more than 120,000 units of products per year, for the amount of 20 million dollars.
The enterprise manufactures more than three thousand different modifications of ball valves. The flexibility of production allows us to design and manufacture products both in accordance with all the main standards of enterprises of the Russian Federation, and under the special requirements of the customer in the shortest time. Every year, dozens of new modifications of ball valves are added to a wide range of manufactured products, designed to meet new requirements.
Ball valves
- Flange, welded, threaded, nippel or any combinations thereof
- Manual control or actuator
- Aboveground or underground valves
- Products of IС Enerpred-Yardos meet the standards of the largest gas and oil companies of the Russian Federation, such as Gazprom, Transneft, Rosneft, Lukoil and others.
The company also manufactures gate valves.
Production
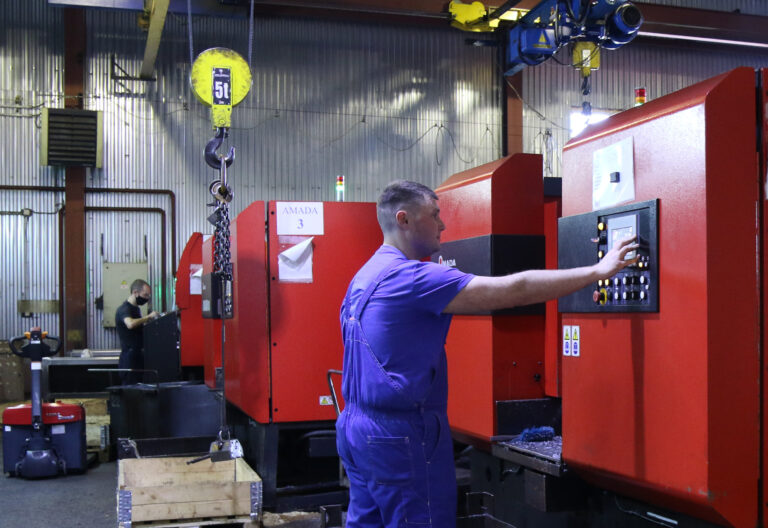
modern machinery
The Enterprise is equipped with modern machinery, it has a closed process from cutting materials to painting. Cutting area equipped with AMADA bandsaw centers
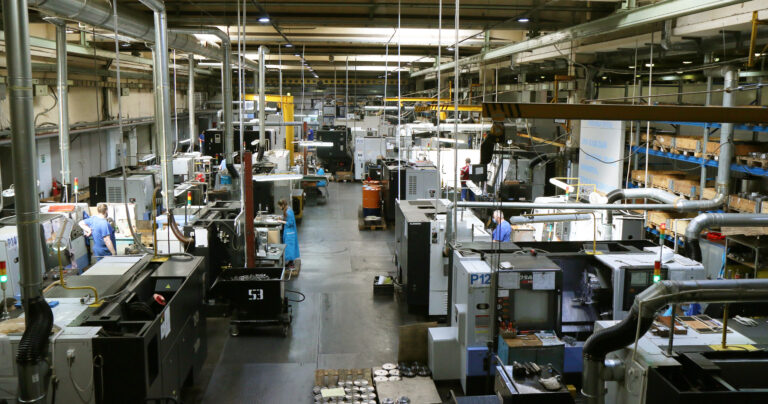
turning & milling departmenTS
There are 44 Doosan high-speed machining centers in the turning department, and 7 Hartford vertical milling centers and 9 Doosan horizontal machining centers in the milling department. The availability of these facilities for metalworking allows us to carry out large orders of both standard products and products of special designs.
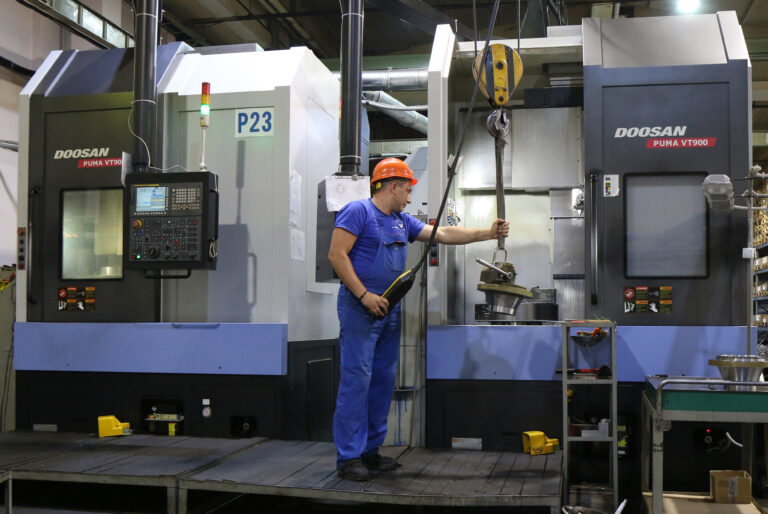
The maximum weight
The maximum weight of workpieces of manufactured parts is up to three tons.
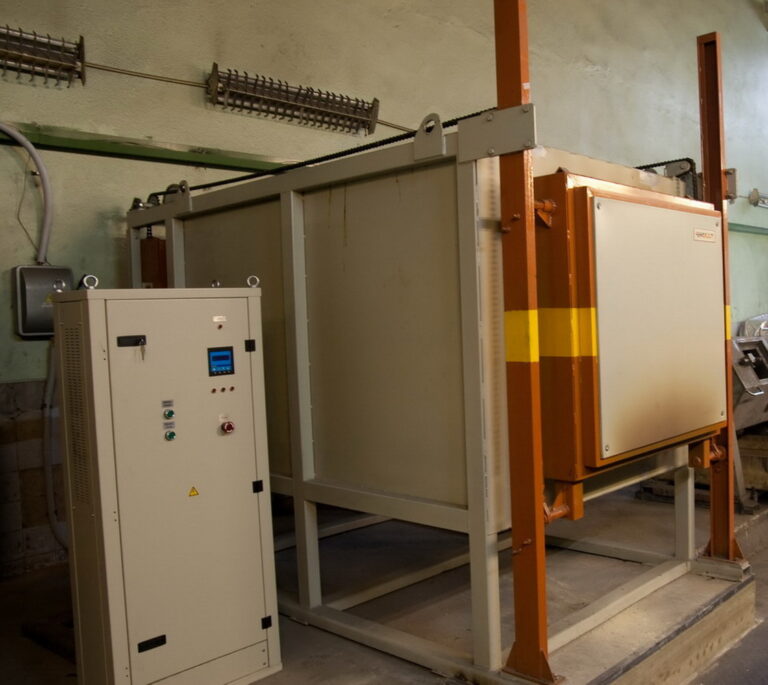
Metal processing
Metal processing is carried out with tools from leading manufacturers such as Sandvik, Iscar and others. Furnaces in the heat treatment area allow carrying out all the necessary heat treatment processes for steel.
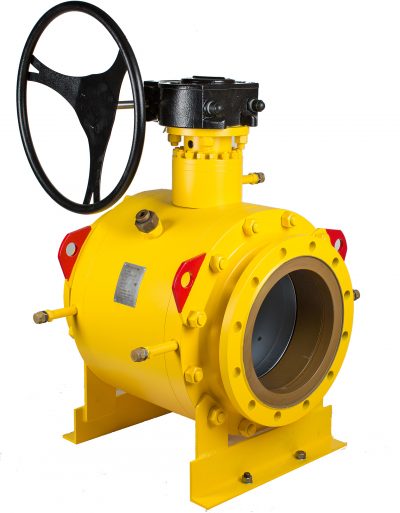
The painting area
The painting area provides for an application of anti-corrosion coatings to products of both aboveground and underground versions. The painting technology for finished products meets the requirements of all major oil and gas companies of the Russian Federation and state standards.
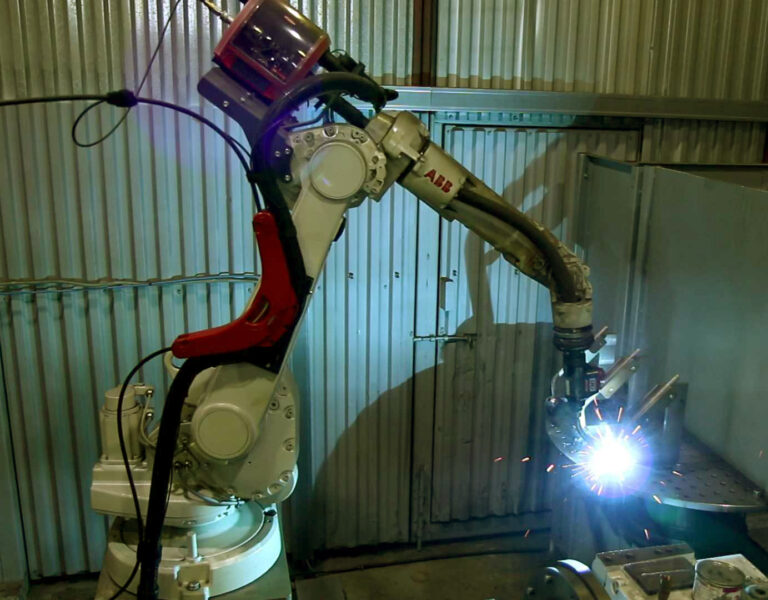
The welding section
The welding section allows manufacturing a wide range of all-welded cranes. Due to the presence of robotic complex, the process of welding products is carried out with maximum quality and speed.
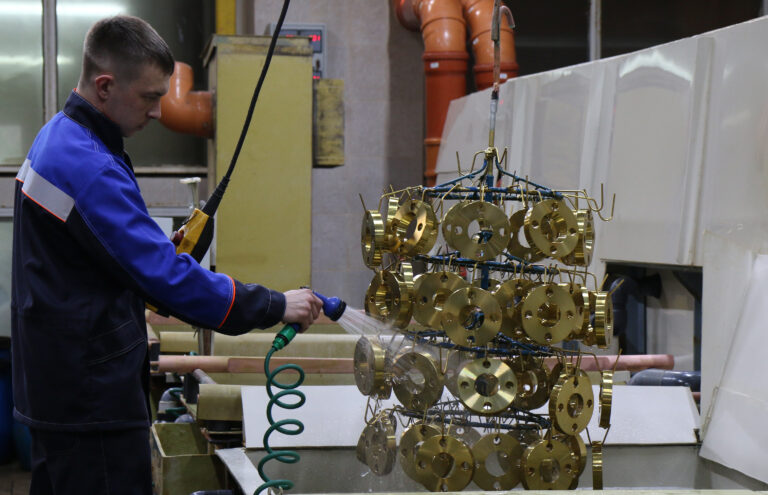
The electroplating section
The electroplating section includes galvanizing and chrome plating lines and line. This makes it possible to cover component parts made of carbon and low-alloy steels with a zinc coating, which significantly increases the corrosion resistance and the lifetime of the finished products.
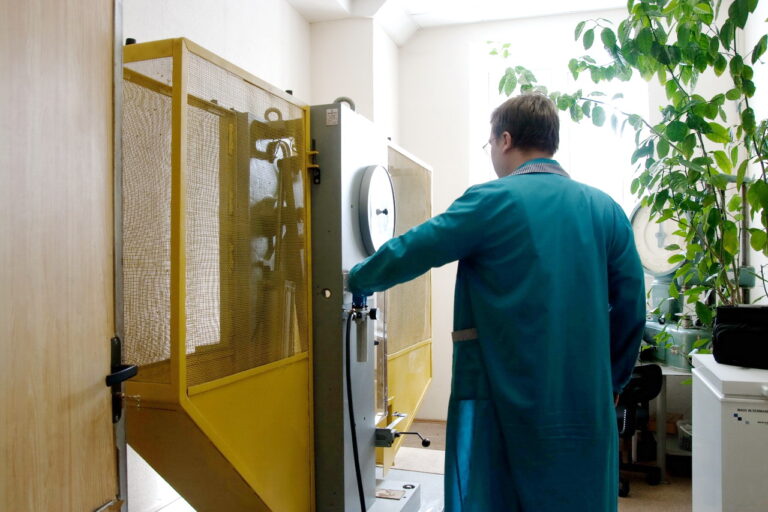
the incoming control
All incoming materials pass the incoming control. The laboratory is equipped with equipment for checking materials for chemical composition, mechanical properties, control of macro and microstructure, tests for intergranular corrosion, ultrasonic flaw detection, capillary flaw detection.
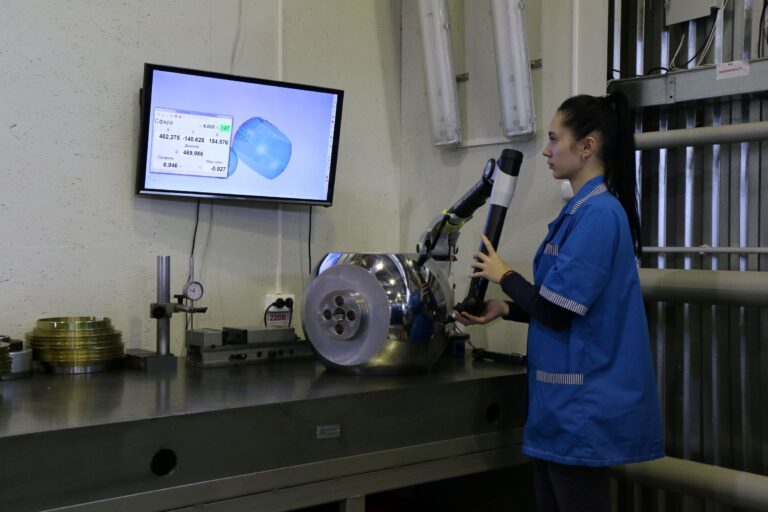
The technical control
The technical control department is equipped with modern equipment. Control is incorporated into the production process and is carried out at every stage of production.
Contacts
Location:
Promploshadka, stroenie 2, Brehovo, Moscow region, Russian Federation, 141544
Postal address:
Post Box #8, Moscow, Russian Federation, 124527